Discharge printing is the block printing method of choice for certain patterns and designs. We turn to this process to create several of our hand block printed collections of linens, and so today we’re stepping out from behind the curtain to introduce you to this form of Indian woodblock printing.
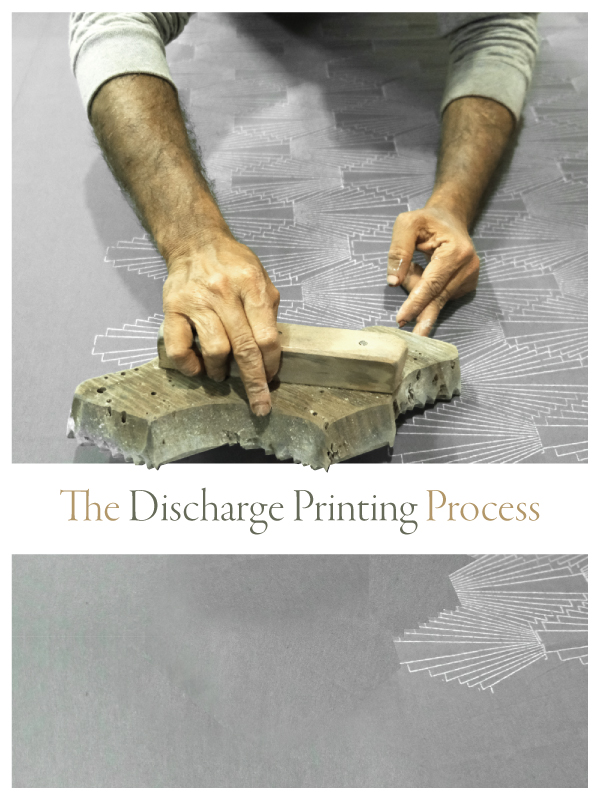
What is discharge printing?
Sometimes referred to as extract printing, discharge printing is a special block printing process. In discharge printing, the artisan removes color from a piece of fabric, creating a lightened effect to create and reveal a pattern.
Applying the design in discharge printing
The process begins with fabric dyed in a rich, saturated hue. Next, the artisan dips a carved wooden block into a bleach paste and stamps the block onto the dyed fabric. Doing this bleaches the pattern onto the dyed ground.
Interestingly, the bleach paste does not immediately lighten the fabric upon contact. As the paste dries on the fabric, it looks almost transparent. The design is barely visible, and this makes discharge printing a particularly challenging process.
Once our artisans print a given number of pieces, it’s time roll the linens up. Yes, that’s right–the next step in extract printing is rolling the fabric over itself. This happens after the dye and bleach has thoroughly dried. As soon as the linens are dry to the touch, they are carefully spread onto a large clean sheet and rolled into a large roll in three times over.
Of course, you can’t just roll up these carefully handcrafted linens any way the wind blows. In fact, when it comes to discharge printing, the skill lies in prepping the fabric for steaming. Imperfect folding will result in either unattractive streaking or failed bleach activation during the next step (the steaming process). A mistake here will render the entire lot of fabric unusable!
Correct folding ensures evenness of heat and moisture permeating the rolls of fabric to properly activate the chemical that bleaches the fabric. In order for the discharge process to be successful, it’s imperative to fold the linens in a certain way. Our master artisan is in the studio every evening during the discharge printing season, personally supervising the steaming of all our linens.
It’s certainly labor-intensive, but it’s an important step since correct rolling will achieve optimal results.
The magical reveal in extract printing
As soon as the block printed fabrics are folded correctly, they enter a deep drum to undergo the steaming process. Water is poured into the drum—only to about a tenth of its capacity—and heated until it begins boiling. The bottom of the drum has a wire mesh positioned ten inches from the bottom of the drum to ensure that the fabric does not come in contact with the water.
At this point, the base of the drum is packed with about several inches of sacking material to control the amount of steam that percolates through the fabric. Finally, artisans lower the roll of fabric enters into the drum so that steam can circulate through the roll.
But why? Why go through all of these steps of rolling and steaming? Good question!
The controlled heat and moisture from the steam activates the bleaching agent in the beach paste, so when we pull the roll of fabric out from the drum, the pattern appears—just like magic!
We repeat this process over and over again. We do this for every single discharge printed piece of fabric. That’s right—each and every one needs to be block printed, rolled up, and steamed.
As you might imagine, discharge printing requires lots of time, physical work, and attention. In light of this alone, extract printed fabrics feel all the more special.
Extra challenges thanks to Mother Nature
Considering the challenges of discharge printing, it’s easy to see how these block printed fabric collections are extra-special. However, Mother Nature always like to throw in extra challenges, and we’ve learned that this kind of printing highly sensitive to atmospheric humidity.
With that in mind, we can only print our extract printed collections during Jaipur’s hot, dry summer months (spring in the U.S.) Since Jaipur’s summer can reach a scorching 115°F, the steaming takes place in the evening when it’s a little cooler. You can learn more about the weather’s impact on block printing and see when your favorite Saffron Marigold block printed fabrics go on the printing tables here.
(And in case you were wondering, approximately 15 meters of fabric fit in one roll, and we print close to 5,000 meters of fabric using this technique. That’s a lot of steaming!)
Block printed fabrics made with the discharge printing technique
We employ the discharge printing process when we want to create a block printed fabric that showcases a light pattern on a richly-hued ground. Several of our block printed fabric collections came about thanks to the the art and craft of discharge printing. Take a look and see if we created your favorite print with this age-old method of block printing.
Istanbul
Rhythmic details, arabesque forms on a deep indigo ground on the main print. An exotic and elegant date palm pattern on the complementary.
Pacific Blue
Ivory waves and ocean-inspired motifs on a rich indigo ground.
Victorian Lilac (Discontinued)
A floral trellis print on a dusty purple ground.
1920 (Discontinued)
A modern and energetic geometric print on a suave, charcoal grey gound.
Starry Nights
A boho batik print of star-like patterning on a deep indigo blue ground.